Economy
Fluenta Installs Technology to Reduce Gas Flaring at Dangote Refinery
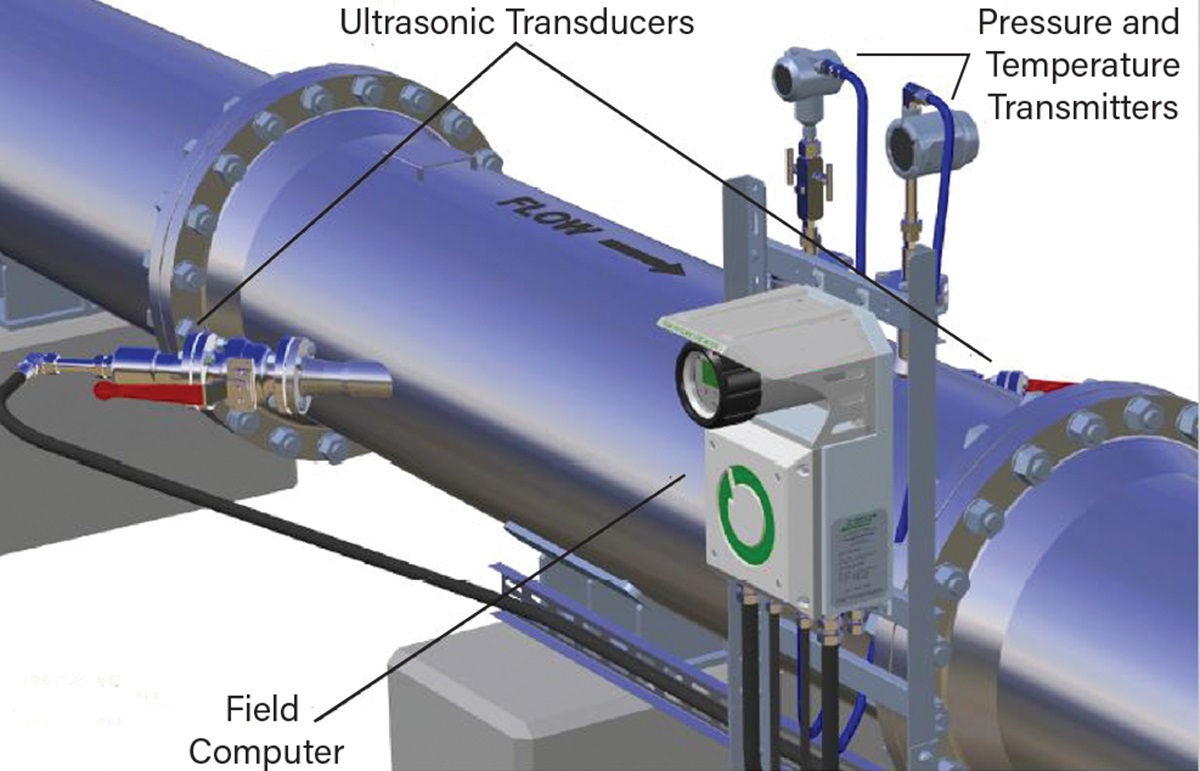
By Adedapo Adesanya
Ultrasonic sensing technology company, Fluenta, has completed work on the Dangote Refinery in Nigeria, Africa’s biggest oil refinery, installing 18 ultrasonic flare gas meters on large pipelines around the plant.
This company is using its technology to aid Nigeria’s flare gas reduction efforts and with Dangote Refinery set to begin operations soon, according to its management recently, this could be a step to fix inaccurate measurements of gas flaring.
Nigeria currently imports refined petroleum products for its use, even though it is Africa’s biggest oil producer and with Dangote Refinery, the world’s largest single-train refinery capable of refining 650,000 barrels of oil per day, the country will be able to meet its daily fuel supply requirements, with a daily surplus of 38 million litres of refined products, already earmarked for export.
Nigeria is positioning itself as a world leader when it comes to reducing its emissions and flaring – the controlled burning or combustion of excess or waste gases that cannot be processed or captured for productive use – is a safety and environmental practice employed in the petroleum industry to prevent the release of potentially harmful or combustible gases into the atmosphere.
Flare measurement in a refinery is essential, from a regulatory and environmental law compliance perspective, and for accurate emissions monitoring.
Fluenta spent more than four months working with its exclusive Nigerian representative, Daptem Engineering, and the Dangote project team to deliver a workable, accurate and reliable flare measurement solution.
Measuring flaring accurately can be a challenge due to installation as the wide variety and sizes of pipelines, which ranged from 18” to 90” diameters presented a unique engineering challenge. Larger pipelines make it difficult to measure accurately as the acoustic pulse has further travel which could weaken it and lead to less accurate readings.
In addition, flared gas expelled through these pipelines is high in CO2, a particularly difficult gas to measure using ultrasonic technology.
The team implemented a multitude of innovative, bespoke solutions, each considered on a case-by-case basis, to ensure the accuracy of the system.
Under current Nigerian law, companies refining oil and gas must pay a tax for flared gas, to encourage an overall reduction in flaring, underlining the importance of Fluenta’s accurate, trustworthy flare measurement and management.
Speaking on this task, Mr Radek Kurkowski, director at Fluenta noted that “Flare gas measurement and control is vital to ensure compliance with environmental regulations and to help identify potential safety hazards. This is especially true at a plant on this never-before-seen scale and with the world’s largest flare pipe.
“Delivering this solution meant some close work with our local partner and the client project team, and we are delighted with the end result – which will support bringing energy security to Nigeria and the wider African region.
“Our team used a range of state-of-the-art technology, adapted meter software and special pipe gaskets and ball valves to deliver the pipe flare gas measurement solution.”
“Fluenta’s work stands as a testament to the power of innovation, creative teamwork and a desire to always meet the client’s needs. We are extremely proud to support the domestic security of energy supply in Nigeria,” he said.
Economy
Legend Internet Plc to List N11.3bn Shares on Nigerian Exchange

By Aduragbemi Omiyale
An Abuja-based Internet Service Provider (ISP), Legend Internet Plc, will list its shares on the main board of the Nigerian Exchange (NGX) Limited.
The listing is expected to take place on Thursday, April 24, 2025, Business Post has gathered.
To mark this, the NGX is organisation an event tagged Facts Behind the Listing for the management of the organisation to inform capital market stakeholders of its numbers and operations.
The executive management team and its issuing house, Finmal Finance Services Limited, will share valuable insights into the company’s strategic vision, growth trajectory, and the anticipated impact of this listing on its operations and market positioning.
Before this, the team will be honoured with a closing gong ceremony, an event to close trading activities at the stock exchange for the trading session.
Legend Internet is an exclusive experience of premium multimedia services built on the foundation of an ultra high speed fibre optic internet connection.
The company delivers the best in Internet, payments, voice, mail and home management, all working together to give customers instant access to the things that matter most – anywhere, anytime.
It was learned that Legend Internet is bringing to the stock exchange a total of 2 billion ordinary shares of 50 Kobo at a unit price of N5.64.
The equities of the firm will increase the market capitalisation of the bourse by N11.3 billion.
Economy
IMF Downgrades Nigeria’s Economic Growth to 3.0%
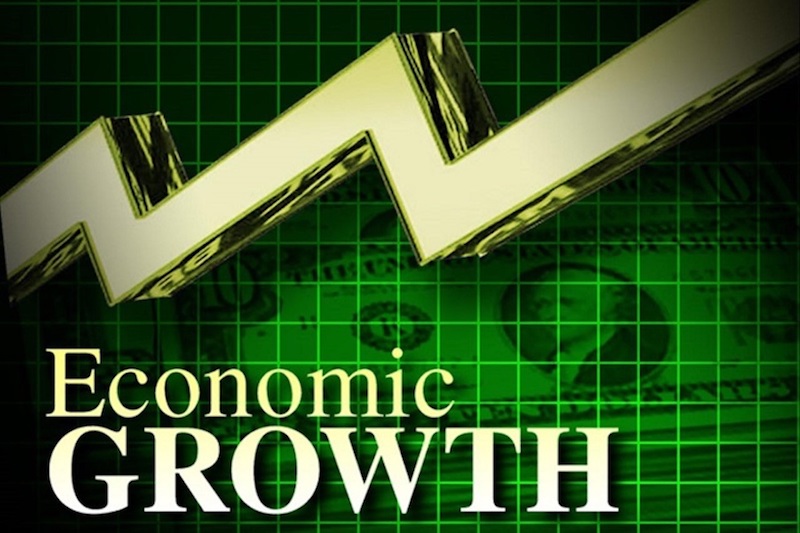
By Adedapo Adesanya
The International Monetary Fund (IMF) has projected that Nigeria’s economy would grow by 3.0 per cent in 2025, a downgrade from the 3.2 per cent project by the organisation earlier this year.
According to its latest World Economic Outlook report released on Tuesday, the Bretton Wood institution said the downgrade was due to recent tariffs move by the US under President Doland Trump.
“Since the release of the January 2025 WEO Update, a series of new tariff measures by the United States and countermeasures by its trading partners have been announced and implemented, ending up in near-universal US tariffs on April 2 and bringing effective tariff rates to levels not seen in a century.” it noted.
The organisation also projects a 2.7 per cent growth rate for the country in 2026.
The global financial institution noted that while Nigeria faces significant challenges, particularly with inflation, forex volatility, and weak infrastructure, recent policy adjustments, such as the partial unification of exchange rates and removal of fuel subsidies, could enhance investor confidence and stimulate economic activity if properly implemented.
The IMF warned that the US tariffs on its own is a major negative shock to global growth.
“The unpredictability with which these measures have been unfolding also has a negative impact on economic activity and the outlook and, at the same time, makes it more difficult than usual to make assumptions that would constitute a basis for an internally consistent and timely set of projections,” the April outlook said.
The IMF added that the swift escalation of trade tensions and extremely high levels of policy uncertainty are expected to have a significant impact on global economic activity.
Based on this, it projected that global growth is projected to slow to 2.8 per cent in 2025 and 3 per cent in 2026—down from 3.3 per cent for both years in the January 2025 WEO Update, corresponding to a cumulative downgrade of 0.8 percentage point, and much below the historical (2000–19) average of 3.7 per cent.
Economy
Tinubu’s Economic Reforms Poorly Timed, Lacked Critical Safeguards—Yemi Kale

By Adedapo Adesanya
Renowned economist, Dr Yemi Kale, says Nigeria must recalibrate its economy through disciplined reforms, forward-looking governance, and people-centred development.
Mr Kale, a former head of Nigeria’s statistics bureau and now Group Chief Economist at Africa Export-Import Bank (Afreximbank), gave this advice at the 2025 Vanguard Economic Discourse, where he delivered a keynote address that examined Nigeria’s current economic hardship and offered a compelling and urgent roadmap toward sustainable recovery and shared prosperity.
According to the economist, Nigeria is grappling with both external shocks and internal structural fragilities: from global inflationary pressures to domestic policy missteps.
“Business as usual is no longer an option,” he quipped, warning that slowing growth, commodity volatility, rising protectionism, and geopolitical instability are compounding Nigeria’s vulnerabilities.
“From exchange rate volatility to eroding investor confidence, Nigeria finds itself navigating a storm with limited buffers,” he explained.
He critiqued the removal of fuel subsidies, FX rate unification, tax overhauls, and monetary tightening, leading to surging inflation, currency depreciation, contracting investment, and intensifying socioeconomic hardship, noting that while the reforms instituted by President Bola Tinubu were necessary steps toward a rules-based economy, they were poorly sequenced and lacked critical safeguards.
“Most of Nigeria’s economic hardship is not caused by unforeseen events but by policies introduced without adequate safeguards. Public trust is built not just by making policies—but by implementing them with foresight, fairness, and firmness,” he submitted.
The economist then outlined a clear, actionable framework to transition Nigeria from macroeconomic fragility to resilient, inclusive growth revolving around three pillars: macroeconomic stability, economic diversification, and social investment and inclusive governance.
He noted that restoring confidence begins with fiscal discipline, transparent FX management, and tighter coordination between monetary and fiscal authorities.
“The first pillar is macroeconomic stability. Macroeconomic stability is not an outcome—it is a prerequisite. Nigeria must rebuild investor and citizen confidence by addressing fiscal imbalances, taming inflation, and restoring exchange rate credibility.”
He noted that this can be done via enforcing tax reform, curb leakages, and ensure budget credibility, empowering the central bank with operational independence and clear mandates, tackling inflation through supply-side reforms—particularly in agriculture and logistics, maintaining a transparent, market-reflective exchange rate supported by non-oil exports and reserve buffers, as well as creating a predictable investment climate that encourages long-term capital formation.
“The second pillar is economic diversification. Diversification is no longer optional. Nigeria’s dependence on oil exposes it to external volatility and fiscal instability. We must rapidly expand our productive base,” adding that core focus should be on agriculture, manufacturing, services and digital economy, small businesses, and infrastructure.
“The third and final pillar is social investment and governance. True growth is people-centered. It must deliver meaningful improvements in the lives of Nigerians across all demographics and regions.”
Dr Kale emphasised that key focus areas include the need to expand social safety nets to protect vulnerable populations from systemic shocks, improve access to basic services—housing, healthcare, electricity, water, and strengthen education through curriculum reform, teacher training, and vocational pathways.
He also advocated fostering entrepreneurship and digital inclusion, particularly for youth and women, deepening institutional trust through anti-corruption enforcement and policy continuity, and usage of digital governance to increase transparency, reduce leakages, and improve service delivery.
“Inclusive growth is not just a social ideal—it is a strategic economic necessity,” he said.
-
Feature/OPED5 years ago
Davos was Different this year
-
Travel/Tourism9 years ago
Lagos Seals Western Lodge Hotel In Ikorodu
-
Showbiz2 years ago
Estranged Lover Releases Videos of Empress Njamah Bathing
-
Banking7 years ago
Sort Codes of GTBank Branches in Nigeria
-
Economy2 years ago
Subsidy Removal: CNG at N130 Per Litre Cheaper Than Petrol—IPMAN
-
Banking2 years ago
First Bank Announces Planned Downtime
-
Sports2 years ago
Highest Paid Nigerian Footballer – How Much Do Nigerian Footballers Earn
-
Technology4 years ago
How To Link Your MTN, Airtel, Glo, 9mobile Lines to NIN